What are Thermal Spray Carbide Coatings and HVOF?
Thermal spray, also known commonly as High-Velocity-Oxygen-Fuel (HVOF) coatings contain tungsten, chromium, and sometiumes nickel or cobalt alloys forming so-called carbides after application. Respecitvely these are most commonly tungesten-carbides (WC) or chromium-carbides (Cr3C2), these are a compound-mixture of a metal and a carbon, and the mixture of the two leads to a elevated hardness often exceeding 1000HV.
With the thermal spray process, a fuel and oxygen are mixed, fed into a combustion chamber, and ignited. The gas produced in the combustion chamber has an extremely high temperature and pressure and is ejected through a nozzle at supersonic speeds. Base-material powder is injected into the high velocity gas stream and direct at the substrate / object to be coated. The result is a coating that has low porosity and high bond strength, which provides it with wear and corrosion resistance. One of the benefits of this process is that extremely dense and hard coatings can be produced at relatively low temperatures, so as to not affect the base material it is applied to.
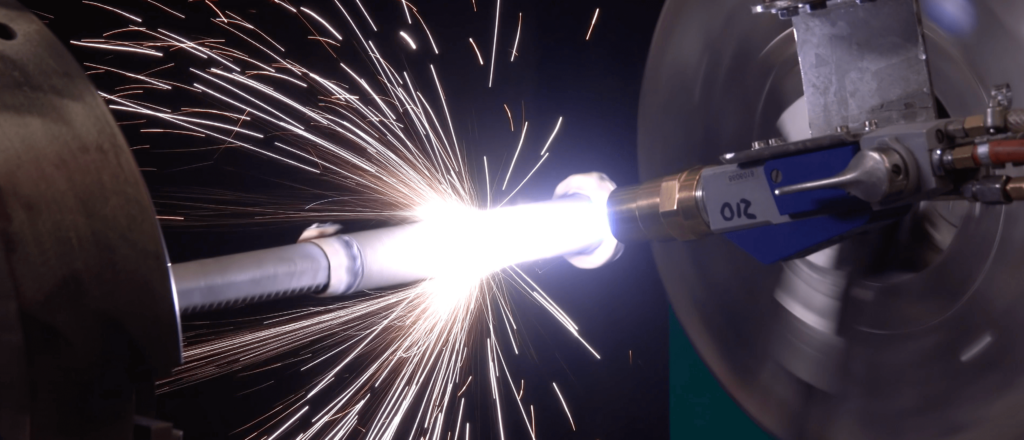
Alloys and their Applications
In order to achieve optimal coating & extension of equipment life, a variety of alloys can be used for the spraying process. Some commonly used materials include:
Materials | Elements | Application |
Tungsten Carbide: | WC | HVOF Tungsten Carbide coatings are extremely dense, well bonded and can be applied to a high thickness if required. These coatings are recommended for components that are subject to wear. |
Tungsten Carbide-Cobalt-Chrome: | WC-Co-Cr | HVOF Tungsten Carbide-Cobalt-Chrome coatings are more wear resistant in most applications than Tungsten Carbide coatings and are more corrosion resistant because of the Chromium content. These coatings recommended for applications with abrasive or sliding wear and are exposed to some corrosion, and are an excellent alternative to hard chromium plating. |
Tungsten Carbide-Nickel Superalloy: | WC-Ni | HVOF Tungsten Carbide-Nickel Superalloy coatings produces a well bonded coating with a high level of wear resistance to abrasive grains, hard surfaces, and fretting. These coatings are ideal for hydraulic rods, ball valves, drilling, and saltwater applications. |
Chromium Carbide: | Cr3-C2 | HVOF Chromium Carbide coatings have high microhardness and are well bonded. These coatings are ideal for providing resistance to solid particle erosion, abrasion, and tribocorrosion at elevated temperatures. |
What are the benefits of this type of coating?
Thermal Spray (HVOF) coatings are perfect for protecting parts that are susceptible to damage from wear and corrosion.
For example, a lot of gas & generation components are subjected to a high amount of tensile stress from flexing and sliding wear and corrosion due to the presence of salts. Spraying parts with an HVOF coating offers protection from wear and corrosion resistance superior to chromium plating. There are many benefits of the HVOF such as:
- High density & bond strength with the base material.
- Improved hardness and toughness.
- Higher coating thickness capability than other thermal spraying processes.
- Increased corrosion resistance.
- Wear protection.
- Low friction surfaces.
- High temperature oxidation resistance.
- Electrical insulation.
- Repair and restoration of damaged components.
Want to learn more? Contact us below: